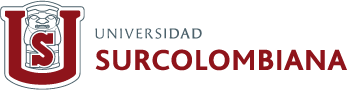
Revista Ingeniería y Región, Volumen 25. 46-59 pp
Enero - Junio de 2021/Universidad Surcolombiana
Artículo de Investigación
Caracterización y redimensionamiento de sistema de bombeo de agua para cultivos acuícolas en finca el Rubí en Aipe-Huila
Characterization and resizing of the water pumping system for aquaculture crops in El Rubí farm at Aipe-Huila
Luis Fernando Arias Ramos
https://orcid.org/0000-0002-9843-5066
Ingeniero Mecánico de la Universidad Antonio Nariño.
E-mail: luisferarias11@gmail.com
Fredy Olaya Idarraga
https://orcid.org/0000-0002-4865-5490
Ingeniero Mecánico de la Universidad Antonio Nariño.
E-mail: olaya1982@outlook.com
Juan Gonzalo Ardila Marín
https://orcid.org/0000-0003-4461-7195
Magíster en Gestión Energética Industrial – Instituto Tecnológico Metropolitano. Docente de la Universidad Antonio Nariño
E-mail: juan.ardila@usco.edu.co
*(Autor para correspondencia)
Fecha de envío: 28/10/2020
Fecha de Revisión: 10/11/2020
Fecha de Aprobación: 13/05/2021
DOI: https://doi.org/10.25054/22161325.2780
Resumen
Los sistemas de bombeo permiten la captación y transporte de agua para su uso. Con el estudio de este campo se redujo el gasto energético en su operación. No obstante, no todas las instalaciones tienen en cuenta los criterios técnicos, generando pérdidas económicas y fallas en servicio. El departamento del Huila es el mayor productor de tilapia nacional, en jaulas flotantes o en estanques en tierra en riveras de ríos, siendo necesarios sistemas de bombeo. La finca el Rubí en Aipe, cultiva 120 ton/año de tilapia niloticus, cuenta con 19 estanques abastecidos por el río Bache. El presente proyecto logró la caracterización y el redimensionamiento del sistema de bombeo de la finca. Se determinó el porcentaje de recambio de agua, el caudal y la velocidad en la tubería existente y se calculó la velocidad óptima en succión e impulsión, el Reynolds en cada sección y las pérdidas por fricción en tubería y en accesorios, para determinar la carga total de la bomba y el NPSH disponible. Se encontró que el sistema actual posee instalaciones rudimentarias y obsoletas, y genera pérdidas por desalineación, mal estado de la calza, altas vibraciones y sedimentos que entran por succión. El sistema actual entrega 12405 m3/día con pérdidas de 10.33 m de cabeza. El redimensionamiento consistió en el rediseño de tuberías, selección de transformador, junta de expansión, acople, y filtro, y el análisis estático y dinámico de la calza, con análisis de resonancia y frecuencia natural, y de cimentación, anclajes y lechada, para finalizar con el presupuesto de implementación. Con el nuevo sistema se espera reducir las pérdidas un 41.77% bajándolas a 6.02 m. El nuevo sistema podría disminuir el tiempo de operación de 24 a 11 horas, implicando un ahorro de 20000 kWh/mes (10’000000 COP/mes). 110’072500 COP de implementación retornarían en 12 meses.
Abstract
Pumping systems allow the collection and transport of water for use. With the study of this field, energy expenditure in its operation was reduced. However, not all installations consider technical criteria, generating economic losses and service failures. The Huila’s Department is the national largest producer of tilapia, in floating cages or in inland ponds on riverbanks, requiring pumping systems. The Rubí farm at Aipe, cultivates 120 tons/year of tilapia niloticus, has 19 ponds supplied by the Bache river. This project achieved the characterization and resizing of the farm's pumping system. The percentage of water change, the flow and speed in the existing pipeline were determined and the optimal speed in suction and impulsion, the Reynolds in each section and the friction losses in pipe and accessories were calculated to determine the total load and NPSH available. It was found that the current system has rudimentary and obsolete facilities, and generates losses due to misalignment, poor condition of the skid, high vibrations and sediments that enter by suction. The current system delivers 12,405 m3/day with losses of 10.33 m of head. The resizing consisted of the redesign of pipes, selection of transformer, expansion joint, coupling, and filter, and the static and dynamic analysis of the skid, with analysis of resonance and natural frequency, and of the foundation, anchors and grouting, to finish with the implementation budget. With the new system, it is expected to reduce losses by 41.77%, reducing them to 6.02 m. The new system could decrease the operating time from 24 to 11 hours, implying a savings of 20,000 kWh/month (10,000,000 COP/month). 110,072,500 COP of implementation would return in 12 months.
1. Introducción
Las crecientes demandas de proteínas han obligado a buscar métodos alternativos a la agricultura o la pesca; la acuicultura, como cría, manejo, nutrición y cría de organismos acuáticos útiles, ha sido considerada como tal. La producción acuícola puede mejorar optimizando el uso de los recursos aplicando la ciencia (Izquierdo & Carrillo, 1997). La cantidad de recursos acuáticos capturados del medio ambiente se ha estancado en los últimos 20 años, y podría esperarse que la producción acuícola represente la mayor proporción del suministro total de pescado en el futuro. El pescado es una fuente importante de proteínas y la acuicultura desempeñará un papel cada vez más importante en la seguridad alimentaria futura (Mo, et al., 2018). El departamento del Huila es el mayor productor de tilapia, gran cantidad de proyectos se encuentran ubicados en la represa de Betania en jaulas flotantes, pero un porcentaje considerable lo hace en estanques en tierra a las riveras de los ríos, siendo así necesario un sistema de bombeo que facilite la captación y transporte del líquido hasta donde es requerido para su posterior uso.
El cultivo intensivo de peces requiere un suministro continuo de agua para mantener su calidad y favorecer los procesos fisiológicos de crecimiento y reproducción en los criaderos. Un conocimiento detallado de estos parámetros permite calcular los requisitos de flujo de agua. Estos son críticos cuando se pretende definir la capacidad de producción en un medio acuático (Izquierdo & Carrillo, 1997). El agua se hace circular mediante bombas, las estimaciones del caudal se basan en los requisitos de oxígeno de los peces mediante el agua que fluye hacia el área de cultivo. Se utiliza un balance de masa simple para calcular la tasa de flujo (volumen / tiempo) dividiendo la tasa respiratoria estimada de los peces (masa de oxígeno / tiempo) por la concentración mínima deseada de oxígeno disuelto (masa de oxígeno / volumen). El flujo de agua requerido varía con el tiempo a medida que los peces crecen y cambia la temperatura del agua (Brown, et al., 2016). Para la producción en estanques de tierra bajo el modelo de piscicultura semiintensiva (10 a 15 peces/m2) en estanques con áreas superiores a 2000 m2 se recomienda mantener un recambio permanente del agua entre 10 a 50 L/s (recambios superiores al 9% del volumen por hora) (Sánchez & Salazar, 2007).
Hay varios tipos de sistemas de bombeo que se pueden utilizar para sistemas de acuicultura, por ejemplo, estaciones de bombeo o bombas sumergibles, Colt, et al., (2006) evaluaron la capacidad de estos sistemas para operar con éxito en función de la elevación de la bomba, las pérdidas de carga del lado de succión, y la temperatura del agua (Colt, et al., 2006). Igualmente, Moses & Colt, (2018), investigaron la reducción en consumo de energía, los costos de producción y las emisiones de gases de efecto invernadero de sistemas en la ingeniería acuícola; la clave de su investigación fue la reducción de los requisitos de cabeza de la bomba y la mejora de la eficiencia (Moses & Colt, 2018). Otras investigaciones han ido un paso adelante proponiendo el uso de fuentes renovables, por ejemplo, Yahyaoui, et al., (2015) presentaron su diseño y evaluación de un sistema fotovoltaico autónomo para bombeo de agua en aplicaciones agrícolas, Korpale et al., (2016) afirman que el sistema de bombeo de agua agrícola basado en energía solar fotovoltaica es la tecnología más adecuada, estudiaron el uso de paneles solares para alimentar una bomba de agua de 2HP presentando el mismo rendimiento al de la bomba convencional, pero con eficiencia económica mayor; Mohana et al., (2018) evalúan cómo hacer eficiente el sistema de bombeo de agua basado en energía fotovoltaica, mediante simulación vía MATLAB / SIMULINK demuestran la eficacia y viabilidad de su propuesta.
La finca el Rubí se encuentra ubicada en el municipio de Aipe, zona norte del departamento del Huila, en donde se cultiva tilapia de la especie niloticus con una producción de 120 toneladas anual, cuenta con 19 estanques en tierra que son abastecidos de agua por el río bache, en la Figura 1 puede apreciarse una vista panorámica de la finca y la disposición espacial de los lagos sur y norte. Lamentablemente, la finca dispone de un sistema de bombeo que no cumple con los requerimientos técnicos necesarios, se han evidenciado pérdidas de energía y material por haberse puesto en funcionamiento sin un estudio y diseño previo, trayendo consigo problemas en los equipos, reduciendo considerablemente su tiempo de vida por fenómenos no tenidos en cuenta en su operación como la cavitación y golpe de ariete. Este proyecto se enfoca en la caracterización del sistema de bombeo actual y su rediseño teniendo en cuenta su finalidad, altura a vencer y caudal requerido.

Figura 1. Vista panorámica de lagos sur y norte. Fuente: Google Maps.
2. Materiales y métodos
El proyecto se desarrolló bajo los enfoques descriptivo y cuantitativo. Descriptivo inicialmente cuando se observaron y recolectaron datos del sistema de bombeo actual y cuantitativo posteriormente cuando se calcularon parámetros de diseño respecto a la tubería, elección de bomba y tipos de accesorios. En la fase documental se identificó el caudal y la presión necesaria para abastecer adecuadamente los lagos, así mismo se revisaron los criterios de diseño aplicados en el sistema hidráulico actual, para detectar las fallas que afectan el funcionamiento de este y se realizó la recolección de datos de campo necesarios para la ejecución de la siguiente fase. En la fase de aplicación se realizaron cálculos a partir de los datos recolectados, para la correcta elección de la bomba, accesorios y tubería a utilizar. También se tuvieron en cuenta los criterios técnicos para la instalación de las maquinas hidráulicas, como la cimentación, el skid, los anclajes, la alineación y demás. En esta fase también se desarrollaron planos del diseño del sistema de bombeo, se realizó un manual de instalación y se elaboró un presupuesto para una posterior ejecución del proyecto.
Inicialmente se estableció la velocidad óptima en la succión e impulsión, teniendo en cuenta que Mott, (2006) recomienda una velocidad de flujo a la salida de la bomba de 3 m/s, y, para garantizar un desempeño apropiado en la entrada, la velocidad recomendada es de 1 m/s. La velocidad recomendada en la línea de succión es de 0.7 a 1.5 m/s (Mott, 2006). Según criterio de Bonnet, se obtuvo el diámetro mínimo que ha de tener la tubería con la Ec. (1).
Ec. (1) |
Para hallar el espesor de la tubería, se realizaron los cálculos con los diámetros nominales de la tubería (OD), para tener una presión de diseño de referencia y así ser exactos con el cálculo de las velocidades del fluido dentro de la tubería, las pérdidas, la carga total sobre la bomba y la potencia efectiva. El Número de Reynolds se calculó de acuerdo con la Ec. (2). Siendo D el diámetro interior de la tubería comercial seleccionada y 𝜼 la viscosidad cinemática.
Ec. (2) |
El factor de fricción para cada sección de tubería es un parámetro adimensional necesario para predecir la pérdida de carga dentro de la tubería debido a la fricción. Como la tubería es de acero entonces se tomó como una superficie rugosa con un coeficiente ε = 1.50E-06 y para la estimación del factor de fricción se empleó la ecuación de Swamme y Jaín Ec. (3).
Ec. (3) |
Ahora se procedió a evaluar las pérdidas por fricción en tubería, la pérdida de energía debido a la fricción que ejerce el fluido sobre las paredes e internamente entre sus partículas depende, como se comentó arriba, del material del cual está construido el conducto y de la velocidad del flujo, para calcular las perdidas por fricción en la tubería se utilizó la ecuación de Darcy, Ec. (4).
Ec. (4) |
En cuanto a las pérdidas en accesorios, al igual que sucede en la conducción a través de la tubería, se encuentra una resistencia en válvulas y acoplamientos, estos elementos pueden ser modelados como tramos de tubería con una longitud equivalente (Le) según su diámetro. Así, las pérdidas secundarias por accesorios en succión y descarga asociadas a válvulas, filtros, reducciones y otros accesorios, deben ser tenidas en cuenta a la hora de calcular la potencia que debe ser suplida por la bomba, la Ec. (5) permitió calcular un coeficiente de resistencia en accesorio dado el fT de la tubería equivalente.
Ec. (5) |
Y para calcular la cabeza pérdida en accesorios dado dicho coeficiente de fricción se empleó la Ec. (6) que resulta ser una adaptación de la ecuación de Darcy.
Ec. (6) |
Con este dato se procedió a evaluar la carga total de la bomba, es decir la potencia que debe ser suministrada para vencer el total de las resistencias y poder suministrar el caudal requerido para el proyecto, para hallarla se tuvo en cuenta el criterio de Bernoulli que hace referencia a que cuando la aspiración se realiza a presión atmosférica está se cancela con la de descarga, ya que la descarga se hará también a presión atmosférica. Igualmente se cancelará la velocidad del fluido en la succión bajo el supuesto de reposo, pues la velocidad del río Bache será considerada despreciable en comparación con la velocidad que adquiere el fluido al ser succionado. Así la expresión para cabeza agregada de Bernoulli se reduce a Ec. (7). Siendo la diferencia de alturas equivalente a la altura geodésica del sistema.
Ec. (7) |
Y con este conocimiento se siguió con la evaluación de la cabeza neta disponible en succión (NPSHd), esta es la diferencia entre la presión del líquido en el eje del impulsor y la presión de vapor del líquido a la temperatura de bombeo, para ello se conocen los datos para el cálculo de presión atmosférica a la altura en msnm en la que se encuentra la estación de bombeo. Se estimó la presión atmosférica (patm) y se procedió al cálculo de la NPSHd mediante la Ec. (8).
Ec. (8) |
Donde ρ es la densidad del agua a la temperatura de succión, ΔHs es la cabeza de succión negativa, hL son las pérdidas en la succión, y pv es la presión de vapor de agua a la temperatura de succión. A continuación, y con base en los datos obtenidos por la carga asumida por la bomba, se calcularon las presiones que van a ejercer los componentes dentro del sistema, y de allí la potencia útil o efectiva (Pe), es decir la potencia que la bomba le trasmite al fluido, se prevé con la Ec. (9).
Ec. (9) |
Para la selección de la bomba hidráulica se requiere que el NPSHd sea mayor al NPSH requerido (NPSHr) para seleccionar los requerimientos mínimos a cumplir de una bomba, los fabricantes ofrecen las curvas características de sus referencias. Luego de seleccionar la bomba se procedió igualmente con la selección del motor y el transformador dadas las especificaciones de los equipos requeridos. Otro accesorio de montaje es el acople omega entre la bomba y el motor, este debe ser capaz de transmitir el torque generado por el motor eléctrico. El fabricante de Acoples Raptor de Dodge establece un método para el cálculo y selección del acople en sus catálogos, este método involucra la potencia en HP, un factor de servicio que depende de la aplicación y para bombas centrífugas resulta de 1.00, y las RPM (ABB, 2020).
A partir del redimensionamiento analizado se procedió al diseño detallado de todo el grupo hidromecánico, en esta fase se realizaron los cálculos mecánicos y diseños a partir de los datos obtenidos, así como simulaciones y comprobación de resultados utilizando software de diseño CAD-CAE (Solidworks®) haciendo uso de su simulador de cargas estáticas y dinámicas por elementos finitos para verificar con resultados numéricos los resultados analíticos, además se propusieron las modificaciones necesarias para mejorar la eficiencia del sistema propuesto.
Para seleccionar el material de la tubería, y calcular su espesor, se empleó la Ec. (10). Donde el espesor nominal (tnom) depende de la presión de diseño (p), el diámetro exterior de la tubería (D), el esfuerzo permisible en tensión (S) del material, el factor de calidad de la junta longitudinal (E), y el factor de corrección (Y) con base en el tipo de material y la temperatura. Los datos para el cálculo del espesor de la tubería fueron obtenidos de (ASME, 1998).
Ec. (10) |
Una vez se conoce el espesor nominal de la tubería requerido se seleccionó el material óptimo a utilizar y la cédula (SCH) que debe tener, esto se hizo basado en las normas DIN 1626 y ANSI/ASME B31.1 que establecen los tipos de material para las tuberías según su temperatura de operación y aplicación. Se seleccionó la tubería según el SCH calculado en relación con el comercial, para ellos la norma ANSI establece un método de acuerdo con la Ec. (11), donde X = 12.5 para el tipo de tubería seleccionado.
Ec. (11) |
Con base en el resultado obtenido para cada una de las referencias seleccionadas, en el software de diseño Pipedata-pro®, se establecieron las dimensiones específicas para los análisis posteriores.
Se continuó con la selección de la junta de expansión, este es un accesorio flexible que se monta en las tuberías para absorber los movimientos causados por dilatación térmica y/o vibración mecánica facilitando el montaje de válvulas y equipos. Para la selección de estas juntas se consultó el catálogo técnico de Flexilatina® (Flexilatina, 2017). El filtro es un accesorio importante para proteger a la bomba de posibles daños en el impeler por atascamientos o golpes de elementos sólidos debido a la succión de sedimentos provenientes del río Bache. Este filtro se seleccionó a partir del caudal requerido por el sistema (Copersa, 2018), y con la condición de que fuera de tipo autolimpiante para evitar las paradas del sistema de bombeo por las limpiezas que se le deban hacer a este accesorio.
Para el diseño del skid o estructura base, elemento que soporta los componentes hidromecánicos principales (motor y bomba), se identificaron dos tipos de cargas: estática y dinámica. Primero se realizó el análisis estático, el tipo de carga a sujetar según Norton, (2011), se definió la carga de clase 1 para el análisis estático del skid, ya que es una carga estática de forma constante. Una vez se definieron las medidas y geometrías exactas se procedió a realizar el diseño del skid, para ello se utilizó el software CAD-CAE. Para el material del skid se propuso acero ASTM A36 laminado en caliente, esta norma abarca láminas, barras, vigas, canales, etc. Además, sus aplicaciones son la construcción de puentes, edificios y otros usos en estructuras en general (DEACERO, 2020). La ficha técnica con las propiedades del material y las medidas comerciales según el fabricante del canal C6X13 seleccionado para la aplicación se encuentran disponibles en DEACERO, (2020).
Para el análisis por elementos finitos (FEA) se definen 5 puntos fijos a los dos lados de la superficie inferior, estos son los anclajes de la estructura a la cimentación. También se le proporcionan al software los datos de fuerza en cada zona que se ejercen sobre la estructura y las propiedades del material, se selecciona un modelo isotrópico elástico lineal para el material. Además, se procedió a realizar un análisis dinámico del Skid. La estructura del skid también experimenta cargas dinámicas, debido a que está soportando máquinas de tipo rotativas. Estas pueden generar desplazamientos de la estructura en los ejes X, Y y Z. Además, allí se presente una fuerza de torque debido a las RPM a las que gira el eje del motor. Estos sistemas cargados dinámicamente también experimentan cargas por vibración, las cuales tienen su origen en diferentes causas. Si los elementos que se utilizan en la estructura fueran infinitamente rígidos, no habría vibraciones en la estructura. Por el contario los materiales tienden a tener cierta elasticidad por ende tiende a deformarse cuando se le aplica una fuerza. Por ello este sistema se analizó mediante el desarrollo de un estudio FEA en SolidWorks® siguiendo la teoría del movimiento armónico simple, el cual se compone de un sistema masa - resorte. Se establecieron los puntos de apoyo y las cargas fijas generadas por el peso de la bomba y el motor, y, de nuevo, las propiedades mecánicas del material. De todas formas, dentro de este análisis dinámico, también es importante evaluar la resonancia y frecuencia natural de la estructura, para efectos de que la estructura del skid no entre en resonancia, debido a que coincidan algunas de sus frecuencias naturales con la frecuencia a las que funcionan las maquinas rotatorias ya que estas generan una excitación de tipo oscilatoria sobre la estructura.
El fabricante del motor eléctrico WEG, establece evaluar la frecuencia de giro del motor, el doble de la frecuencia del giro del motor y la frecuencia eléctrica del motor, y menciona que de acuerdo con la norma DIN 4024-1, la frecuencia natural de la base de primer orden debe estar fuera del rango comprendido entre 0.8 y 1.25, las demás frecuencias naturales deben estar fuera de rango entre 0.9 y 1.1 veces cualquiera de las frecuencias potenciales de excitación. Para el motor disponible la frecuencia, por su velocidad angular de giro, equivale a 29.66 Hz, así las frecuencias potenciales de excitación serán la frecuencia de giro del motor 29.66 Hz, el doble de la frecuencia del giro del motor 59.33 Hz, y la frecuencia eléctrica del motor 60 Hz. En el estudio FEA se evaluaron 15 modos de vibración que se puedan presentar en la estructura, de acuerdo con las cargas dinámicas soportadas, estableciendo las frecuencias naturales de la estructura y las coordenadas en las que se presentan.
La cimentación es la base de la estructura que soporta el conjunto bomba – motor, la cual debe adsorber vibraciones y proporcionar un soporte rígido a la estructura se diseñó de acuerdo con la Norma ACI351.3R-04 que establece tipos de cimentaciones para maquinarias. En el caso de la aplicación actual y con la configuración bomba centrifuga – motor eléctrico, el tipo de estructura más adecuado y recomendado por los fabricantes es la cimentación tipo bloque (American Concrete Institute, 2004). La marca Hidrostal, fabricante reconocido de bombas recomienda una losa de concreto tipo bloque sin zapata de base 1-3-5 (cemento, arena y ripio), asegurándose de que el tratamiento del concreto debe cumplir con la norma DIN 1045. El grosor de la placa dependerá de las necesidades de cada instalación y de la disposición del suelo (Hidrostal, 2009). La cimentación constituye el elemento intermedio que permite transmitir las cargas que soporta una estructura al suelo subyacente, de modo que no rebase la capacidad portante del suelo y que las deformaciones producidas en éste sean admisibles para la estructura. Por tanto, para realizar una correcta cimentación habrá que tener en cuenta las características geotécnicas del suelo y además dimensionar el propio cimiento como elemento de hormigón, de modo que sea suficientemente resistente (Ministerio de Fomento - España, 2019). Las dimensiones del bloque de concreto deben extenderse al menos 50 mm más allá de la estructura base de la bomba y 100 mm de los pernos de anclaje del skid. El espesor de la cimentación no deberá ser inferior a 60 cm. El borde superior de la cimentación debe mantenerse a unos 30 cm del nivel natural del terreno o de la superficie en que se encuentre. La ubicación y el tamaño de los orificios para los pernos de cimentación deben coincidir con los que se muestran en el diagrama de montaje incluido con el paquete de datos de la bomba. El peso de la cimentación debe ser entre dos y tres veces el peso de la bomba.
En cuanto a los anclajes, los pernos de cimentación que se utilizan comúnmente para este tipo de montaje son los de tipo manguito (Barba & Sánchez, 2015). Y, por último, el grout es un material autonivelante empleado en rellenar espacios estrechos entre un anclaje y la perforación, y entre una placa base y la fundación sobre la que se apoya, tal que al endurecer es capaz de transmitir uniformemente los esfuerzos hacia la fundación, permitiendo el óptimo funcionamiento de todo el conjunto. El grout experimenta tensiones estáticas y dinámicas, que pueden ser uniaxiales, biaxiales o triaxiales (Arancibia, 2006). La empresa fabricante de bombas Hidrostal sugiere el uso del grout tipo cementicios (mortero). Este tipo de grout proporciona una resistencia a la compresión superior a los 180 kg/cm2 y a un menor costo, ideal para actual aplicación.
Para finalizar, se procedió a la cotización de los componentes sugeridos, los procesos de manufactura y la mano de obra requerida para implementar el diseño sugerido y justificado como resultado del estudio realizado.
3. Resultados y discusión
3.1 Caracterización del sistema de bombeo actual
El sistema de bombeo actual emplea 3 tipos de tubería según su etapa (Succión y descarga). La longitud de la tubería de succión es de 13.3 m siendo esta de 14”. Para la descarga se divide en 2 siendo una parte de 12” con una longitud de 18.7 m y una tubería de 6” que va hacia los lagos sur con una longitud aproximada de 100 m, como dato adicional se halló una altura geodésica de 21.2 m. Los lagos sur y norte tienen un volumen total de 205519 m3 y se requiere un caudal de recambio al 9% norte (Q = 16419 m3/día) y 5% sur (Q = 1154 m3 /día), para Q = 17573 m3/día, o 0.2005 m3/s. Este caudal se estableció una vez se calculó el volumen de cada lago, la descripción puede apreciarse en las Tablas 1 y 2, luego se evalúan diferentes porcentajes de recambio de agua en cada lago y se escoge el recomendado.
Tabla 1. Volumen lagos norte.
![]()
×
|
|
Fuente: Autores
Tabla 2. Volumen lagos sur
![]()
×
|
|
Fuente: Autores.
La velocidad en tubería existente se estableció con el modelo de continuidad, en la tubería de succión V = 2.019 m/s, mientras en la tubería de impulsión V = 2.750 m/s. Según el concepto técnico DTN (Dirección Territorial Norte)no. 495 de 2016 emitido por la CAM (Corporación Autónoma Regional del Alto Magdalena), informa que se realizóla visita el 29/02/2016 y se verificó que la captación se realizaría por bombeo de las aguas del río Baché, margenderecha; se georreferenció el sitio de la captación arrojando un valor de 839243N – 862383E, a una altura de 398msnm. El predio está ubicado en la coordenada 862530E – 839208N, altura de 412 msnm. Se aforó el caudal de lafuente arrojando un valor de 2394 L/s.
Tras la evaluación se encontró que el sistema actual posee instalaciones rudimentarias y obsoletas, y genera pérdidas por desalineación, mal estado de la calza, altas vibraciones y sedimentos que entran por succión. El sistema actual entrega tan sólo 12405 m3/día, que es menor al caudal recomendado dada la producción en la finca. Y evaluando el diseño actual se establecieron pérdidas de 10,33 m de cabeza, que, como se explicará más adelante, deben ser asumidas por el sistema de bombeo y terminan en costos por consumos de energía eléctrica que deben ser cubiertos implícitamente por el propietario.
3.2 Redimensionamiento del sistema de bombeo
Dada la necesidad de aumentar el diámetro en la succión para disminuir la velocidad según las recomendaciones de Mott, (2006) se emplea la Ec. (1) y el cálculo arroja Dmin = 17.28”, el cual no es un diámetro comercial, se dispondrá del diámetro comercial siguiente a la medida calculada: 18”, con el que la velocidad V =1.2755 m/s cumplirá con la recomendación. Para la descarga se seleccionan tuberías de 12” y 6” ya que V = 2.5775 m/s en ambas también cumple.
Los cálculos de Re (Ec. (2)) arrojan 5.60E+05 en succión, y 7.95E+05 y 4.08E+05 en cada brazo de la descarga, y dado que Re mayor a 4.00E+03 se considera turbulento así que, según Ec (3), f = 0.1289 en succión y 0.01217 y 0.01371 en los brazos de descarga, respectivamente. De tal manera que la cabeza pérdida en entrada y salida de la bomba, empleando la Ec. (4), viene siendo de 0.0318 m en succión y 0.2448 m y 2.8748 m en cada brazo de descarga.
En el diseño sugerido se propone el uso de tres accesorios en succión: codo 90°, válvula de píe tipo disco – vástago y filtro, que tras los cálculos se estima una pérdida de cabeza de 0.4843 m, mientras en los dos brazos de descarga se sugiere el uso de 2 codos 90°, 1 codo 45°, una T estándar con flujo en el ramal, una válvula de cheque de 12”, una válvula mariposa de 12” y otra de 6”, así que empleando el modelo descrito en las Ec. (5) y (6), se estima una cabeza total pérdida de 2.0038 m. Así la sumatoria total de pérdidas es igual a 6.0195 m.
Así la cabeza que debe ser agregada por la bomba (Ec. (7)) equivale a 27,5582 m. Con la información disponible hasta ahora se establece que, según Ec. (8), NPSHd= 6,8770 m. Y dada una presión de diseño con coeficiente de seguridad de 1.5 igual a 405369 Pa, así que la Pe requerida se estima con la Ec. (9) en 54176 W, es decir 54.18 kW. Para este caso se propone la centrífuga Malmedi Hidromac ETN 10x10x12E graficando el punto de operación en la gráfica de las referencias 250 a 290E, donde se establecen los siguientes valores característicos RPM = 1750 rpm, Potencia = 100 HP, NPSHr= 3.5 m, Eficiencia = 80 % en el punto de operación (Malmedi, 2018).
Procediendo a la selección de motor eléctrico, las especificaciones técnicas mínimas a cumplir son de 100 HP y 1750 rpm. Actualmente la finca dispone de un motor de 125 HP y 1780 rpm que resulta idóneo para la bomba sugerida en el presente estudio. Así que a continuación se realiza la selección de transformador para el motor eléctrico según su conexión, en este caso a una tensión de 440 V trifásicos para un kVA de transformador trifásico equivalente a 111.26 kVA. Se recomienda incrementar la potencia un 15% para efectos de eficiencia y seleccionar el transformador comercialmente más cercano. En este caso se tiene una potencia aparente necesaria de 127 kVA y se selecciona un transformador trifásico de 150 kVA para esta carga (Nuñez, 2013).
El torque calculado fue de 4426 lb.in, por lo cual se seleccionó el acople E40 ya que su torque máximo de 5500 lb.in es superior al torque calculado y necesario en el conjunto motor – bomba (Rexnord, 2014).
Inicialmente se presenta la vista general de diseño, en la Figura 2 se ilustra un diagrama general de diseño donde se dimensionan y acotan la altura a vencer junto con la ubicación y espesor de la tubería y cada componente, en éste se evidencia el recorrido que hace el líquido hasta el primer tanque de descarga donde inicia su recorrido por gravedad.
Mediante la Ec. (10) se supo que el espesor requerido para la tubería de succión es equivalente a 3,595 mm, para las de descarga deben ser 3,214 mm y 2,768 mm, respectivamente. El material que se adapta a los requerimientos es el ASTM A 106 A Acero al carbono (C – Si). La tubería sin soldadura de acero al carbono ASTM A106 se utiliza en aplicaciones industriales que implican bajas y altas temperaturas, incluidas las tuberías de proceso y estaciones bombeo, también es conocida como tubería ASME SA106. A partir de la Ec. (11), para la tubería de succión, se establece tped = 4,11 mm, y para los brazos de descarga tped = 3,65 mm y 3,15 mm cada uno. De acuerdo con los datos disponibles en la ASTM A106, se escoge el SCH 10s para los 3 diámetros de trabajo, puesto que este SCH supera al tped, como lo establece la norma ANSI.
El modelo adecuado de junta de expansión es del tipo JEBA que es fabricado integralmente en EPDM, elastómero que presenta excelentes propiedades de resistencia química, al envejecimiento térmico por exposición a los rayos solares y el ozono. Se aplican en sistemas que operan con presión interna positiva o bajo vacío, lo que la hace apropiada para trabajar en succión o descarga de bombas. Los terminales de juntas de caucho son bridas giratorias en acero carbono dimensionadas según norma ASME b 16.5 clase 150 (Flexilatina, 2017), la presión de operación máxima permisible de 150 psi, supera la presión del sistema establecida anteriormente, así que está dentro de su rango de operación permisible. Se seleccionó el pre-filtro autolimpiante serie 18112 normal 2.500 micras (8 mesh) ya que su caudal máximo de 750 m3/h se adapta al requerido por el sistema.
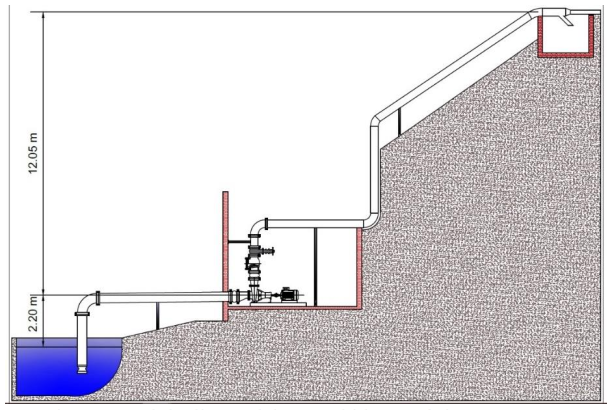
Figura 2. Vista general de diseño del grupo hidromecánico. Fuente: Autores.
Al realizar el diseño adecuado del skid se deben tener en cuenta las medidas y geometrías exactas de los equipos que van a ser instalados, las masas suministradas por los fabricantes del motor eléctrico y la bomba son: motor eléctrico WEG modelo W22 de 691 kg (WEG, 2017) y bomba centrífuga Hidromac ETN 250/290E de 659,5 kg (Malmedi, 2018), las dimensiones generales y la ubicación de sus puntos de anclaje está disponible igualmente en los catálogos. Como resultado del estudio se observa que el límite de deformación máximo de la estructura no supera el límite elástico del material, por el cual es idóneo para ser usado en la instalación de los componentes hidromecánicos. En la Figura 3 se presentan los resultados del análisis FEA del skid, allí puede apreciarse, en escala de contornos, la magnitud del esfuerzo equivalente de Von Mises resultado de la combinación de cargas axiales, flexionantes, cortantes y torsionantes en cada elemento de la estructura, máximo de 2.26E+08 Pa, contrastable con la resistencia a la cedencia del material reportada también allí, de 2.50E+08 Pa. Igualmente, el resultado de este estudio dinámico mediante FEA indicó que el límite de tensión máximo de la estructura no supera el límite elástico del material, por lo que se concluye que soportará las cargas dinámicas que se le aplicarán, máximo de 1.68E+08 Pa, contrastable con la resistencia a la cedencia del material de 2.50E+08 Pa. Y el estudio de vibración arroja que, la menor frecuencia, en el primer modo fue de 104.74 Hz, y la mayor, en el último modo evaluado, fue de 273.58 Hz.
Tras todas las decisiones tomadas y justificadas se establece la propuesta de rediseño del sistema existente proponiendo el presentado en la Figura 4, allí: 1. Bomba centrifuga - Hydromac modelo ETN 250/290E, 2. Acopleomega estándar E40, 3. Motor eléctrico - WEG modelo W22 - 125 HP, 4. Skid - Base del equipo de bombeo, 5. Grouting - 1" de espesor, 6. Cimentación - mínimo 300 mm por fuera de la superficie del suelo, resto de la cimentación empotrada, 7. Superficie del suelo - subestación de bombeo, y 8. Pernos de anclaje - tipo manguito con cuñas de nivelación a cado lado de los pernos.
Al final se establece un costo total del proyecto en 110’072500 COP, donde el costo más representativo es el de la bomba centrífuga en 16’115800 COP, y las válvulas de retención y de compuesta de 12” en 11’235658 y 6’200000 COP, respectivamente, y el filtro autolimpiante en 9’258894 COP.
El principal resultado del redimensionamiento consiste en haber propuesto una alternativa que permite reducir las pérdidas un 41.77% bajándolas de 10.33 m actuales a 6.02 m. Y al aumentar el caudal del sistema de los 12405 m3/día a los 17328 m3/días sugeridos para una producción óptima, el propietario indicó que el caudal actual era suficiente para una producción satisfactoria, así que el nuevo sistema podría disminuir el tiempo de operación de 24 horas/día que está operando actualmente a 11 horas/día, implicando un ahorro de 20000 kWh/mes (10’000000 COP/mes). Esto sucedería porque el sistema de bombeo actual ha presentado consumos de hasta 40000 kWh/mes, considerando que se reducen las horas de bombeo para alcanzar el caudal requerido y que las frecuencias de bombeo dependerán de que todos los lagos estén en producción, se pudo establecer una reducción de horas de bombeo en aproximadamente 9 horas por frecuencia de bombeo.
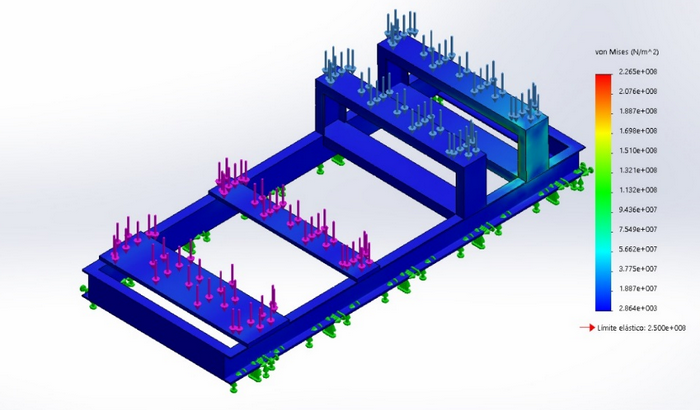
Figura 3. Resultados del estudio FEA del skid: Von-Mises equivalente. Fuente: Autores.
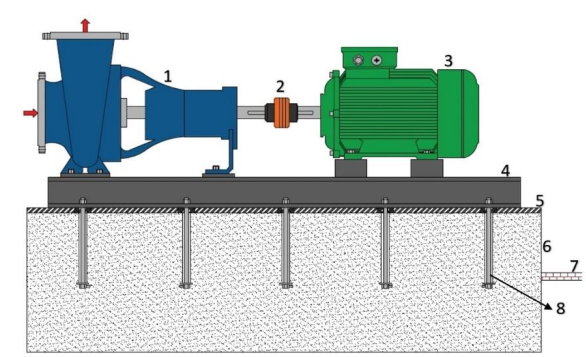
Figura 4. Disposición del equipo de bombeo, cimentación, anclajes y grauting. Fuente: Autores.
Según esto, la inversión establecida, retornarían en tan solo 12 meses como resultado de los ahorros en consumo de energía eléctrica, que de todas formas se verían disminuidos permanentemente tras la implementación de una estrategia apropiada de operación y mantenimiento del sistema de bombeo, que evidentemente incrementaría la rentabilidad del negocio y disminuiría su impacto ambiental en el entorno. La vida útil estimada es de 25 años con su respectivo mantenimiento preventivo.
4. Conclusiones
Se logró proponer una solución a la problemática optimizando el recurso energético, el sistema de bombeo actual entrega 12405 m3/día con un total de pérdidas mecánicas equivalentes a una cabeza de 10.33 m, con el diseño propuesto se pueden reducir estas pérdidas un 41.77% al bajarlas a 6,019 m.
Además, el sistema diseñado puede bombear en 11 horas lo que suministra el sistema actual en 24 horas, y que es considerado satisfactorio para la producción según el propietario de los predios. Así, el nuevo sistema podríadisminuir el tiempo de operación de 24 a 11 horas, implicando un ahorro de 20000 kWh/mes (10’000000 COP/mes).Entonces 110’072500 COP de implementación retornarían en 12 meses.
En cuanto al conjunto motor-bomba se pudo establecer por el diseño que el motor eléctrico posee una eficiencia del 94,16%. La bomba, según su curva característica es capaz de transmitir al fluido un 80% de esa potencia recibida por el motor.
Para la implementación del sistema de bombeo se recomienda realizar la alineación y montaje por personal capacitado, se debe asegurar que sea hecho por personal idóneo con equipos para tal fin, también disponer de la totalidad de los equipos seleccionados ya que estos trabajan en conjunto para un óptimo funcionamiento.
Aunque el sistema eléctrico actual está en funcionamiento, se recomienda el aval de un técnico electricista que certifique la idoneidad de ellos en el sistema.
Se recomienda mejorar el acceso hacia los equipos para comodidad en la instalación y en mantenimientos periódicos. También, el fabricante del pre-filtro autolimpiante serie 18112 establece una verificación periódica de la malla y del funcionamiento del sistema de autolimpieza. Si bien no hay un tiempo establecido para hacer esta actividad, recomendamos realizar esta verificación del estado de la malla en acero inoxidable normal 2500 micras (8 mesh) por lo menos 1vez cada 15 días y de ser necesario sustituir la misma.
5. Referencias bibliográficas
ABB, (2020). ABB Offers a Total Power Transmission Solution. Mechanical Power Transmission. Consultada 22/05/2020. https://new.abb.com/mechanical-power-transmission/dodge-couplings/dodge-elastomericcouplings/raptor-couplings. https://doi.org/10.3403/02586324u
American Concrete Institute, (2004). ACI 351.3R-04 Foundations for Dynamic Equipment. ACI COMMITTEE REPORT. Consultada 22/05/2020. https://worldarchi.com/wp-content/uploads/2019/05/3513R_04.pdf
Arancibia, F. (2006). Grouting: Tipos, Características y Requisitos para su Colocación. Ingeniería y Construcción. Consultada 22/05/2020. https://facingyconst.blogspot.com/2006/05/groutingtiposcaracteristicasy.html
ASME, (1998). Power Piping: ASME Code for Pressure Piping B31 an American National Standard. American Society of Mechanical Engineers. Consultada 25/04/2020. https://www.nrc.gov/docs/ML0314/ML031470592.pdf https://doi.org/10.1115/b31
Barba Barba, K. J., & Sánchez Cevallos, D. D. (2015). Diseño de una Placa Base para una Bomba Centrífuga Tipo DVS J-14X25. Repositorio Escuela Politécnica Nacional. Consultada 22/05/2020. https://bibdigital.epn.edu.ec/bitstream/15000/11360/1/CD-6443.pdf
Brown, T.W., Tucker, C.S., & Rutland, B.L., (2016). Performance Evaluation of Four Different Methods for Circulating Water in Commercial-Scale Split-Pond Aquaculture Systems. Aquacultural Engineering. Vol. 70, pp. 33– 41. https://doi.org/10.1016/j.aquaeng.2015.12.002
Colt, J., Plesha, P., & Huguenin, J., (2006). Impact of Net Positive Suction Head on the Design and Operation of Seawater Pumping Systems for Use in Aquaculture. Aquacultural Engineering. Vol. 35, pp. 239–257. https://doi.org/10.1016/j.aquaeng.2006.03.001
Copersa, (2018). Ficha Técnica. ODIS Prefiltro Autolimpiante Serie 18100. Repositorio Universidad Nacional Abierta y a Distancia UNAD. Consultada 22/05/2020. http://www.copersa.com/es/catalogo/odis-pre-filtros/prefiltros-autolimpiantes-para-aspiraciones-serie-18100/_p:94/
DEACERO, (2020). Ficha Técnica Canales estructurales. Perfiles y Vigas Estructurales. Consultada 22/05/2020. https://www.deacero.com/canales-estructurales
Flexilatina, (2017). Juntas de Expansión en Caucho. Catálogo Técnico. Consultada 22/05/2020. https://flexilatina.com/wp-content/uploads/2017/09/Catalogo-juntas-de-caucho.pdf
Hidrostal, (2009). Manual del Usuario: Instalación, Operación y Mantenimiento. Bomba Centrífuga ISO 2858. Consultada 22/05/2020. https://www.abcingenieria.com/wp-content/uploads/2017/01/manual-bomba-centrifuga2858.pdf
Izquierdo, M., & Carrillo, M., (1997). Optimization of Aquaculture Systems in Spain. Energy Conversion Managment. Vol. 38. No. 9. pp. 879-888. https://doi.org/10.1016/s0196-8904(96)00094-5
Korpale, V.S., Kokate, D.H., & Deshmukh, S.P., (2016). Performance Assessment of Solar Agricultural Water Pumping System. Energy Procedia. Vol. 90, pp. 518-524. https://doi.org/10.1016/j.egypro.2016.11.219
Malmedi, (2018). Bombas Hidromac. Fábrica de Bombas Malmedi. Consultada 25/04/2020. http://bombasmalmedi.com/p159/ETA-/-ETN/product_info.html
Ministerio de Fomento – España, (2019). Documento Básico SE-C Seguridad Estructural Cimientos. Consultada 22/05/2020. https://www.codigotecnico.org/pdf/Documentos/SE/DBSE-C.pdf
Mo, W.Y., Man, Y.B., & Wong, M.H., (2018). Use of Food Waste, Fish Waste and Food Processing Waste for China's Aquaculture Industry: Needs and Challenge. Science of the Total Environment Vol. 2018, pp. 635–643. https://doi.org/10.1016/j.scitotenv.2017.08.321
Mohana Rao, M.J., Kumar Sahu, M., & Kumar Subudhi, P., (2018). PV Based Water Pumping System for Agricultural Sector. Materials Today: Proceedings. Vol. 5, pp. 1008-1016. https://doi.org/10.1016/j.matpr.2017.11.177
Moses, D., & Colt, J., (2018). Impact of Fish Feed on Airlift Pumps in Aquaculture Systems. Aquacultural Engineering. Vol. 80, pp. 22–27. https://doi.org/10.1016/j.aquaeng.2017.12.001
Mott, R.L., (2006). Mecánica de Fluidos. Pearson Educación.626 pp.
Norton, R.L., (2011). Diseño de Máquinas. Pearson – Prentice Hall. 1048 pp.
Nuñez, O., (2013). Selección de Transformadores para Motores. Boletín Mensual Motortico. Consultada 25/04/2020. http://www.motortico.com/biblioteca/MotorTico/2013%20NOV%20-%20Seleccion%20de%20Transformadores%20para% 20Motores%20Electricos.pdf
Rexnord. (2014). Elastomeric Coupling Catalog. Rexnord Company. Consultada 25/04/2020. https://www.rexnord.com/contentitems/techlibrary/documents/4000_catalog
Sánchez Ortiz, I. A., & Salazar Cano, R., (2007). Infraestructura hidráulica para acuicultura: un aporte en la compilación y adaptación del conocimiento ingenieril a la acuicultura. Revista Electrónica en Producción Acuícola, Vol. 2, pp. 246-297. Consultada 25/07/2019. https://revistas.udenar.edu.co/index.php/reipa/article/view/1669/2060. https://doi.org/10.15741/revbio.08suppl.e1181
WEG, (2017). W22 Motor Trifásico. Catálogo Comercial Mercado Latino-Americano. Consultada 22/05/2020. https://static.weg.net/medias/downloadcenter/h60/h24/WEG-w22-motor-trifasico-50044029-brochure-spanishweb.pdf
Yahyaoui, I., Tina, G., Chaabene, M., & Tadeo, F. (2015). Design and Evaluation of a Renewable Water Pumping System. IFAC-Papers On Line. Vol. 48, núm. 30, pp. 462–467. https://doi.org/10.1016/j.ifacol.2015.12.422